India has committed to producing 5 million tonnes of green hydrogen per year by 2030, supported by approximately 125 GW of new renewable generation capacity (CEEW, 2024). Yet behind this high-profile ambition lies a less discussed but arguably more decisive factor: the vast electrical infrastructure required to turn fluctuating renewable electricity into the stable, precisely controlled DC power that electrolyzers need. This is the real machinery that converts photons and winds into hydrogen molecules, and it is expensive, complex, and often invisible in public debates (Iris CNR, 2024).
Today, India’s green hydrogen costs hover between ₹397–₹560 per kilogram ($4.6–$6.7/kg), which is two to three times the cost of grey hydrogen produced from natural gas. Nearly 95% of this cost is tied to capital investment and financing, and within that, 30–50% comes from electrical systems alone. For a single 100 MW PEM electrolyzer project, that means ₹1,000–1,200 crore ($120–145 million) just in transformers, rectifiers, converters, switchgear, sensors, and control systems (CEEW, 2024). In other words, the electrons are not only expensive because renewable power isn’t free, but they are also expensive because they must be processed, stabilized, and delivered with extraordinary precision.
Hydrogen electrolysis is an energy-intensive process, requiring 50–55 kWh/kg H₂ including losses (Iris CNR, 2024). Of this, power conversion losses typically account for 1–2 kWh/kg, equivalent to 2–4% of total energy input.
Technical benchmarks help illustrate what’s at stake:
- Thyristor-based SCR rectifiers achieve >98.5–99% efficiency at full load but suffer poor power factor (<0.7) and up to 30% total harmonic distortion (THD) if not mitigated with filters.
- Active front-end IGBT converters deliver 96–97% efficiency but maintain near-unity power factor and <5% THD (ResearchGate, 2024).
- A 100 MW electrolyzer operating 7,000 hours/year will consume 700 GWh/year of AC input. If conversion losses are reduced from 4% to 2%, the plant saves 14 GWh/year, translating to ₹70–85 crore/year at industrial tariff rates (~₹5–6/unit).
- Ripple reduction is equally critical: PEM stacks degrade faster under >5% DC ripple. High-frequency interleaved DC-DC converters can cut ripple below 1%, extending stack life from ~60,000 to ~80,000 hours (Iris CNR, 2024).
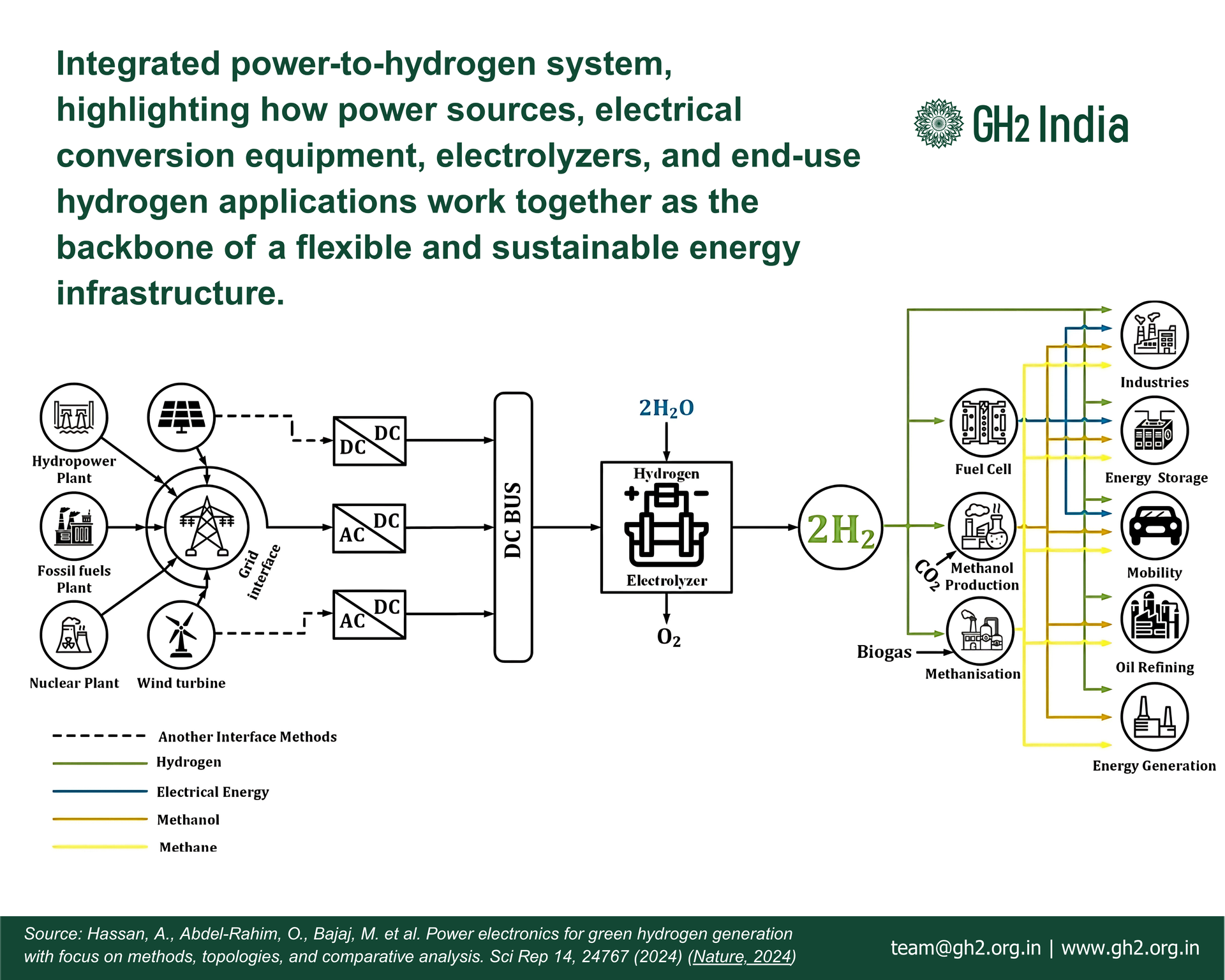
In Germany, the REFHYNE project demonstrated how advanced electrical engineering can transform operations. There, a 10 MW PEM electrolyzer dynamically ramps its load in less than 30 seconds, seamlessly participating in grid-balancing markets while maintaining stringent power quality under IEEE 519 standards. (REFHYNE, 2022)
For India, achieving similar performance will require a shift toward modular, standardized designs. The strategy pioneered at Saudi Arabia’s NEOM megaproject, containerized 5–20 MW blocks of rectifiers, transformers, and controls that scale simply by replication, can unlock enormous efficiencies. If each module delivers >99% rectifier efficiency and power factors above 0.95, scaling from 20 to 200 MW becomes a process of adding modules, not re-engineering the system. India’s industrial base is well-positioned for this approach. The chlor-alkali sector already produces high-current rectifiers and transformers, but the country lacks consistent standards tailored to electrolyzers (REGlobal, 2024). Establishing these norms through the Bureau of Indian Standards could streamline procurement, cut design timelines, and make financing easier.
Grid integration remains another critical frontier. India’s natural advantage of 300+ clear days a year in many regions, and world-leading wind resources also brings volatility. Solar output can swing by ±50% within minutes due to clouds, and grid frequency events exceeding 0.5 Hz deviations occur more than ten times a year. Managing these fluctuations requires not just rugged electrolyzer stacks but sophisticated power electronics and storage buffers. Maximum Power Point Tracking (MPPT) converters can improve renewable utilization by 5–10%, while battery systems sized at 15–20% of electrolyzer capacity can buffer variability and protect equipment from sudden voltage dips (Iris CNR, 2024).
India has already taken early steps in this direction. In Gujarat, Adani’s 5 MW off-grid pilot project uses solar power paired with a battery energy storage system to deliver consistent, high-quality DC electricity. The project has demonstrated that even in fully off-grid configurations, modern converters and smart controls can ensure stable hydrogen output (PV Magazine, 2025). Scaling this experience to 100 MW and beyond, however, will require strong policy support and incentives for hybrid system integration.
Safety is the other pillar that cannot be overlooked. Hydrogen is flammable in concentrations from 4–75% and has an auto-ignition temperature of around 560 °C. In Europe, ATEX and IECEx standards have established clear rules for explosion-proof equipment and rigorous zoning since the early 2000s (IECEx, 2021). In India, regulatory frameworks are still evolving. The Petroleum and Explosives Safety Organisation (PESO) and the Oil Industry Safety Directorate have begun adapting global norms, but many project developers are learning that even a small unapproved UPS cooling fan can create unacceptable risks, an oversight that forced shutdowns in UK pilots.
Looking ahead, digital technologies can play a decisive role in bridging these challenges. India has a globally recognized IT sector and deep experience in advanced analytics. There is a unique opportunity to develop digital twins for electrolyzer electrical systems, creating virtual replicas that simulate converter performance, predict component wear, and schedule maintenance before failures occur. A 100 MW hydrogen plant in the Desert could one day be monitored by AI algorithms that continuously optimize energy flows and detect anomalies. With the right investments, India could become not just a hydrogen producer, but an exporter of advanced control and monitoring solutions.
To seize this opportunity, India needs a clear playbook. First, it must establish BIS standards for 5–20 MW modular electrical blocks, with specifications on efficiency, power factor, and safety. Second, policy incentives like Production-Linked Incentives should be extended to cover SiC-based converters, explosion-proof components, and solid-state transformers. Third, R&D funding under the National Hydrogen Mission should support pilots that demonstrate AI-enabled digital twins and predictive maintenance. Finally, India must invest in human capital, training at least 10,000 engineers in hydrogen plant electrical systems over the next five years.
The story of India’s hydrogen transformation is often told as a race to install solar panels and build electrolyzers. But the real success will be determined, if India can build a system that delivers >97% end-to-end efficiency, <5% THD, and >98% uptime while meeting world-class safety standards, it will be well on the way to reducing hydrogen costs from $5–6/kg today to $1.5–2/kg in the coming decade.
It may sound like engineering detail, but in reality, it is a strategic imperative. With careful planning, targeted incentives, and a relentless focus on quality, India can ensure that its green hydrogen ambitions rest on a foundation as solid as the renewable electrons themselves.
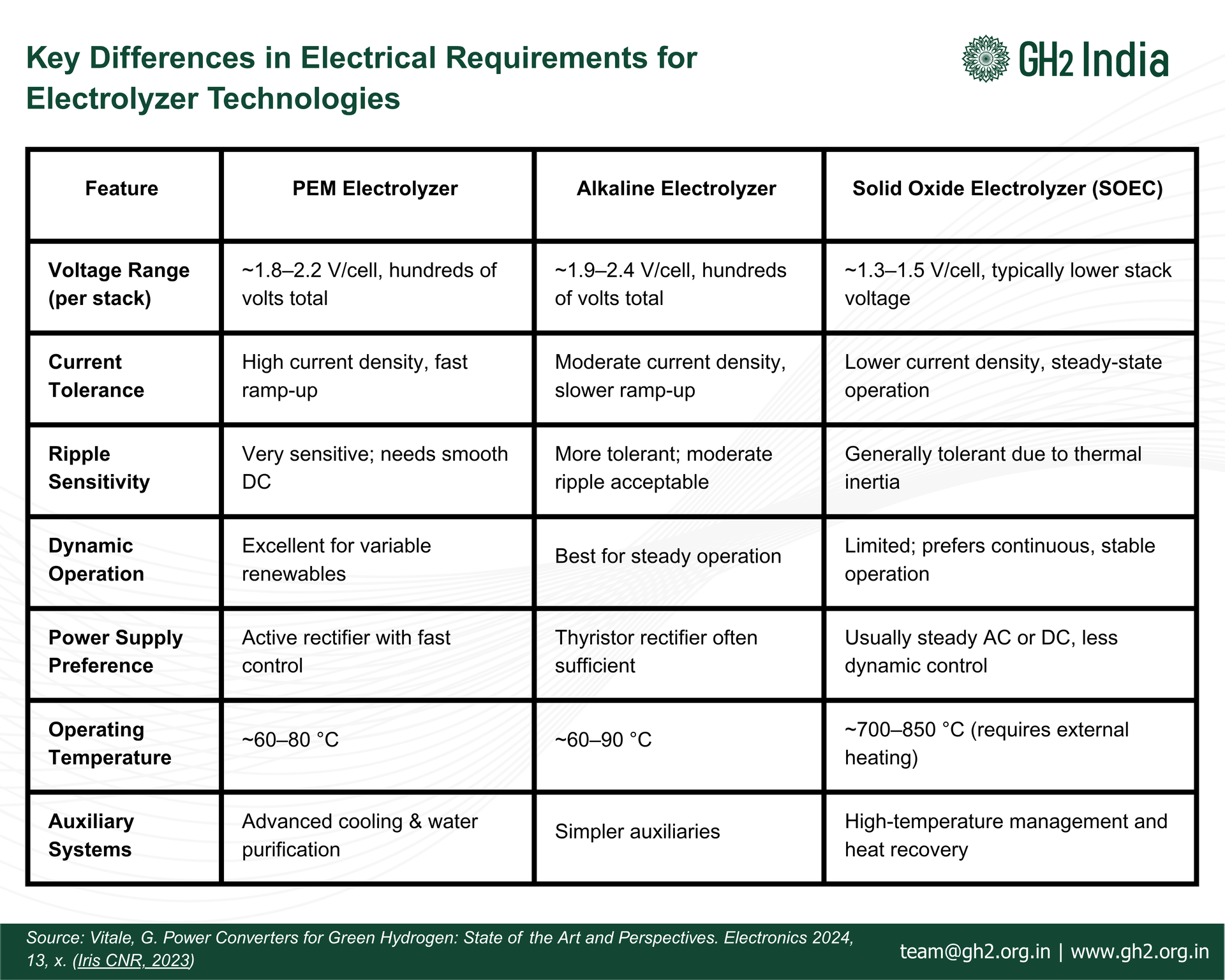
Sources
- CEEW. (2024). How Can Hydrogen Electrolysers Be Made in India? https://www.ceew.in/sites/default/files/how-can-india-indigenise-and-boost-domestic-hydrogen-electrolyser-manufacturing.pdf
- Iris CNR. (2024). Electrolysis Technologies for Hydrogen Production. https://iris.cnr.it/retrieve/0ebd7a0a-d063-48ca-87df-d8085e3e2842/manuscript.v9_rev_IRIS.pdf#:~:text=There%20are%20different%20technologies%20for,21
- Akul Raizada, LinkedIn. (2024). How India Can Scale Electrolyzers for Its 5 MMT Green Hydrogen Goal. https://www.linkedin.com/pulse/how-india-can-scale-electrolyzers-its-5-mmt-green-hydrogen-raizada-vrwte/
- Nature. (2024). Power Electronics for Renewable Integration. Nature Energy, 7(8), 710–712. https://www.nature.com/articles/s41598-024-76191-6?error=cookies_not_supported&code=7ff2f2c8-8f3b-42e5-a72d-e089c65ce009#citeas
- PV Magazine. (2025). Adani’s 5 MW Off-Grid Hydrogen Pilot. https://www.pv-magazine.com/2025/06/24/adani-commissions-off-grid-5-mw-green-hydrogen-plant/#:~:text=Kutch%2C%20Gujarat,powered%20hydrogen%20production
- REFHYNE. (2022). Project Overview. https://refhyne.eu
- IECEx/IEC Standards for Hydrogen https://etech.iec.ch/issue/2023-06/safety-for-hydrogen#:~:text=IECEx%20certification%2C%20which%20has%20been,by%20enabling%20the%20required%20robustness
- MDPI (2024). A Comprehensive Review on the Power Supply System of Hydrogen Production Electrolyzers for Future Integrated Energy Systems. Energies, 17(4), 935. https://www.mdpi.com/1996-1073/17/4/935#:~:text=where%20the%20electrolyzer%20constructs%20the,power%20supply%20in%20the%20future


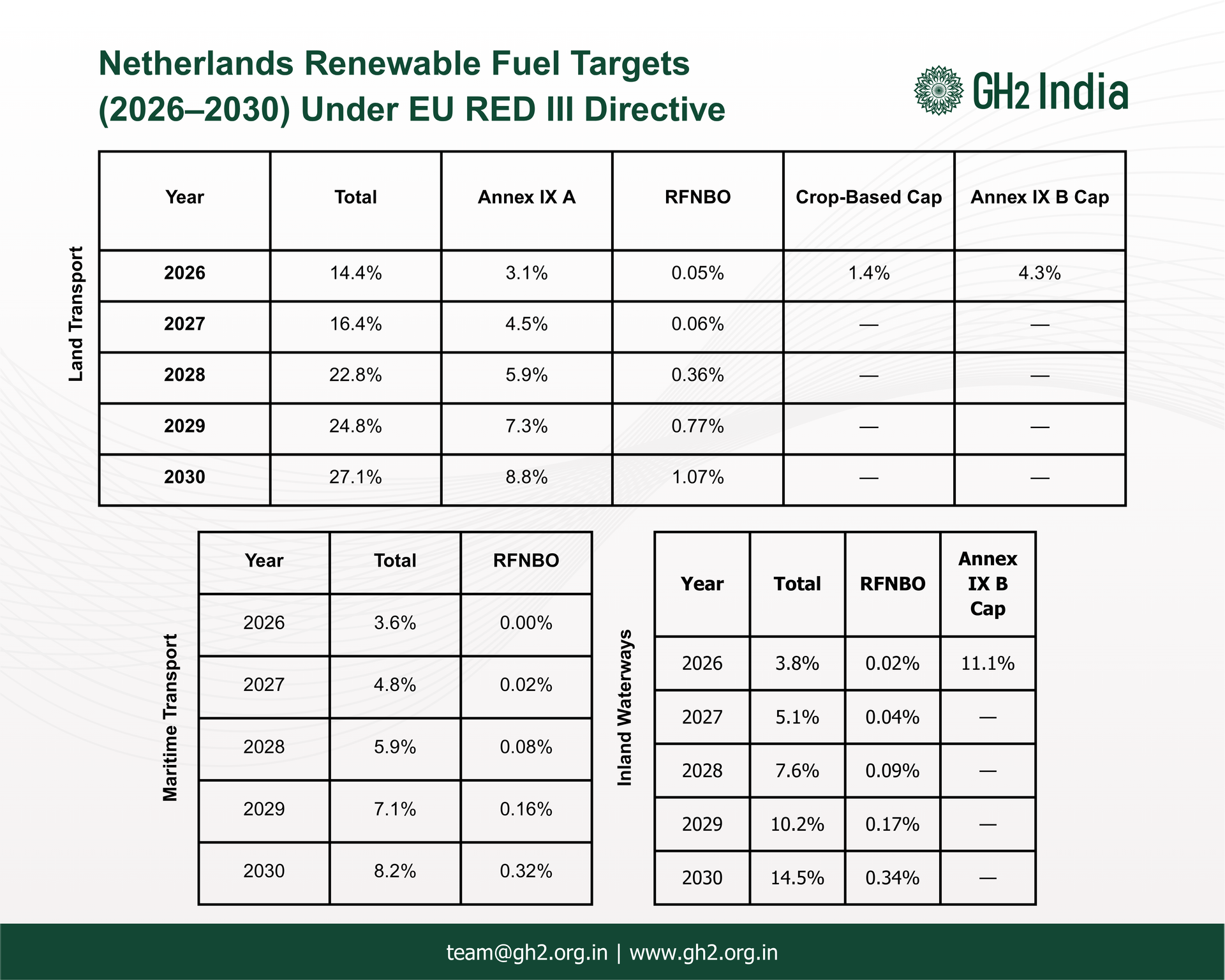
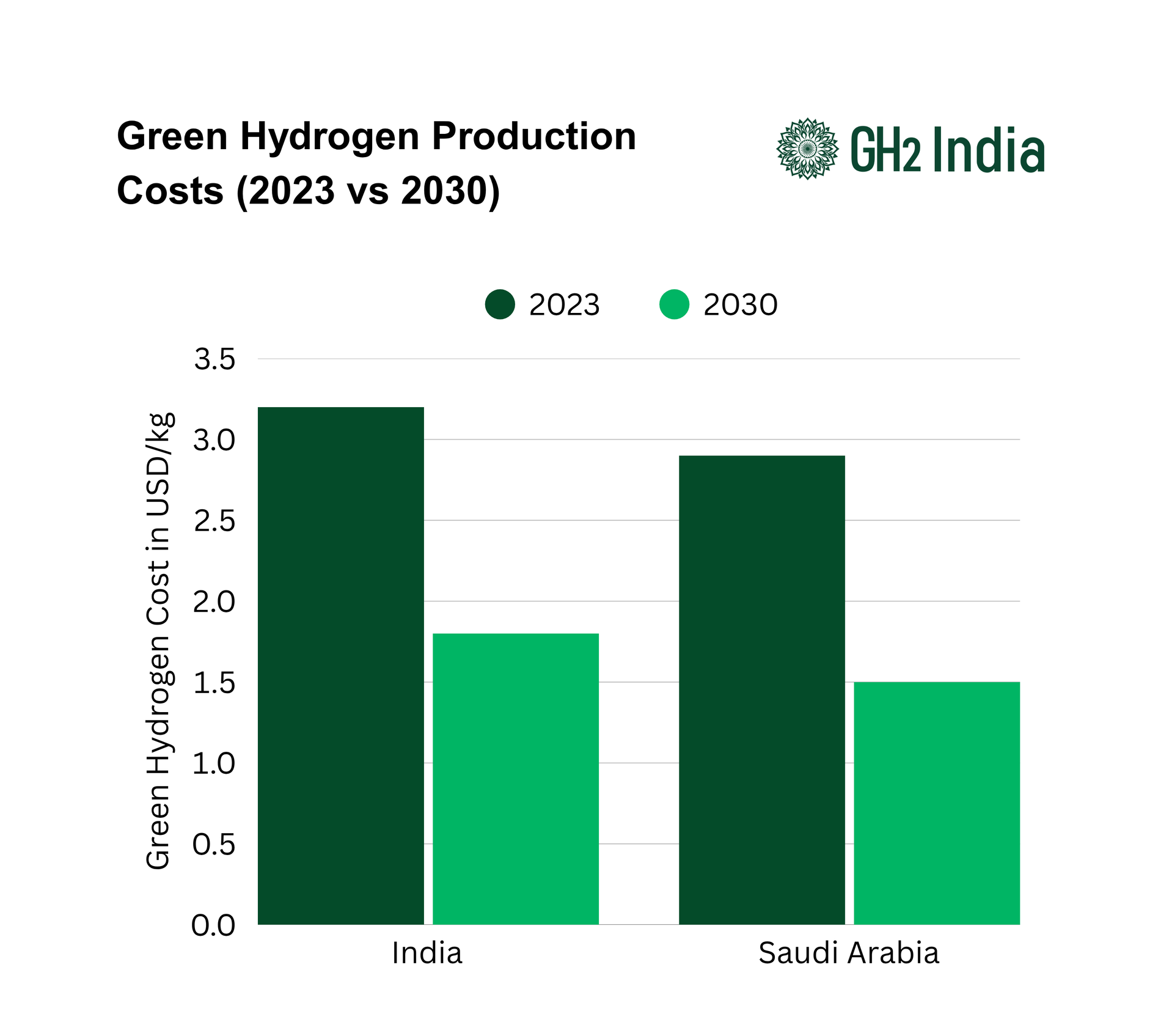
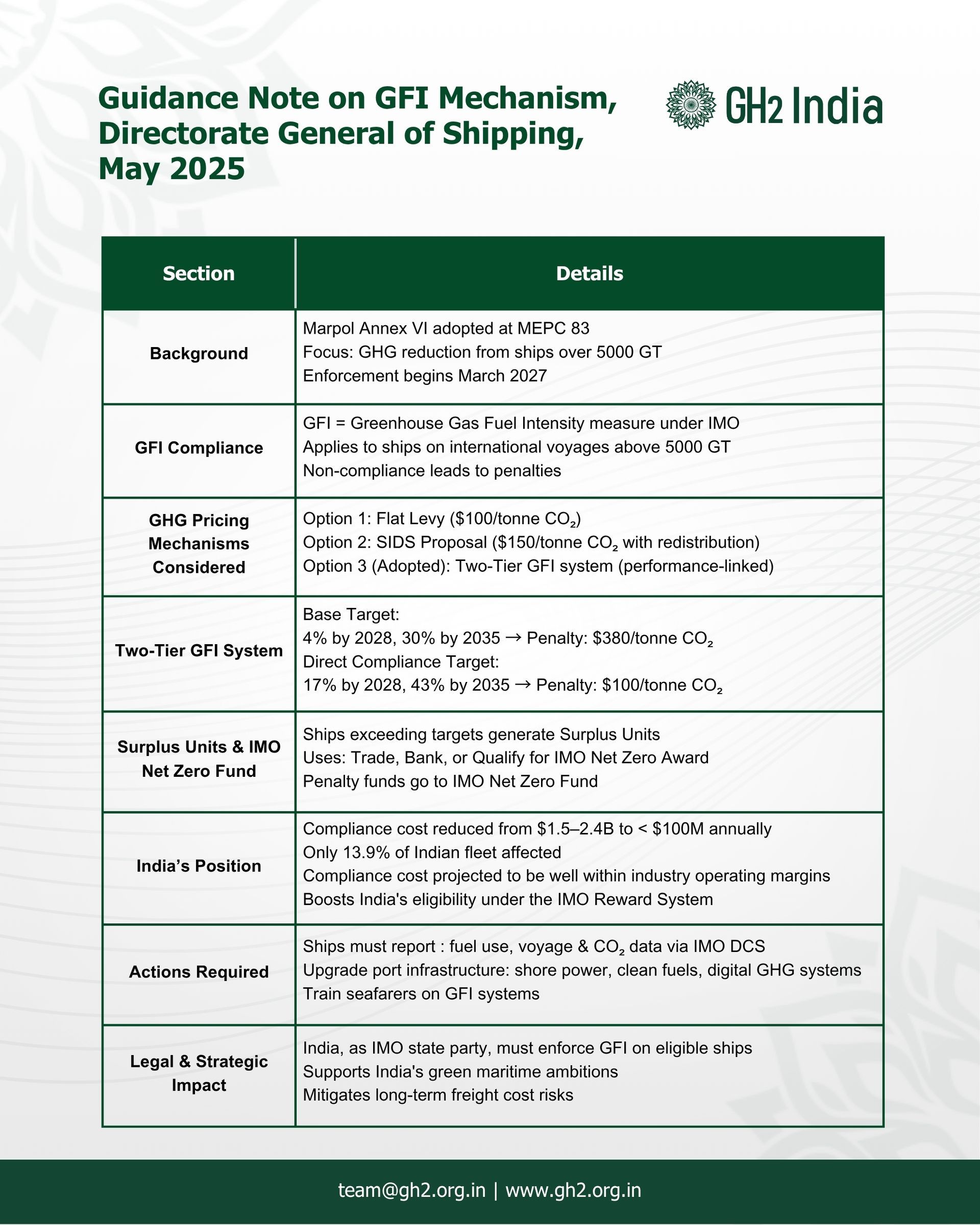
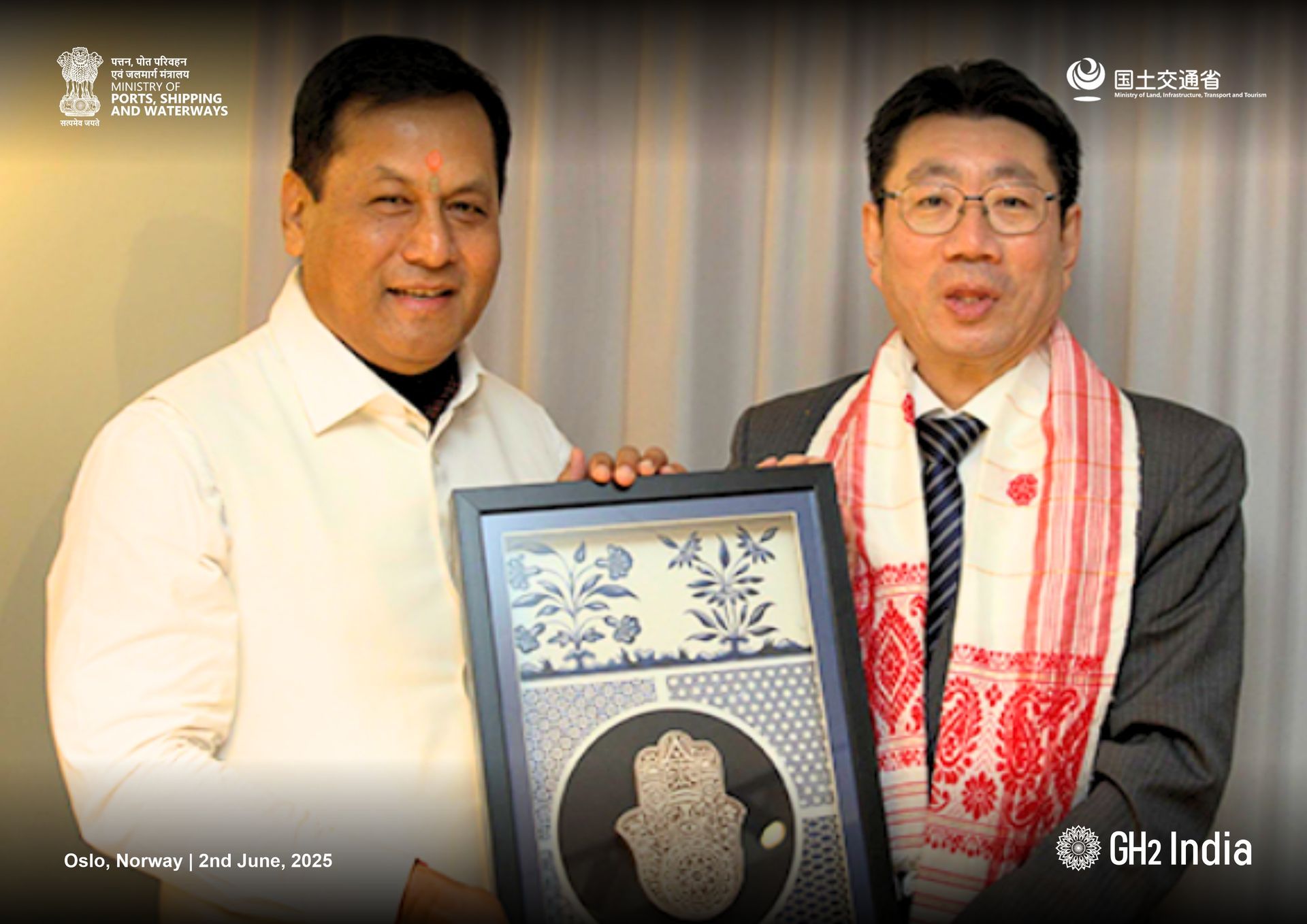
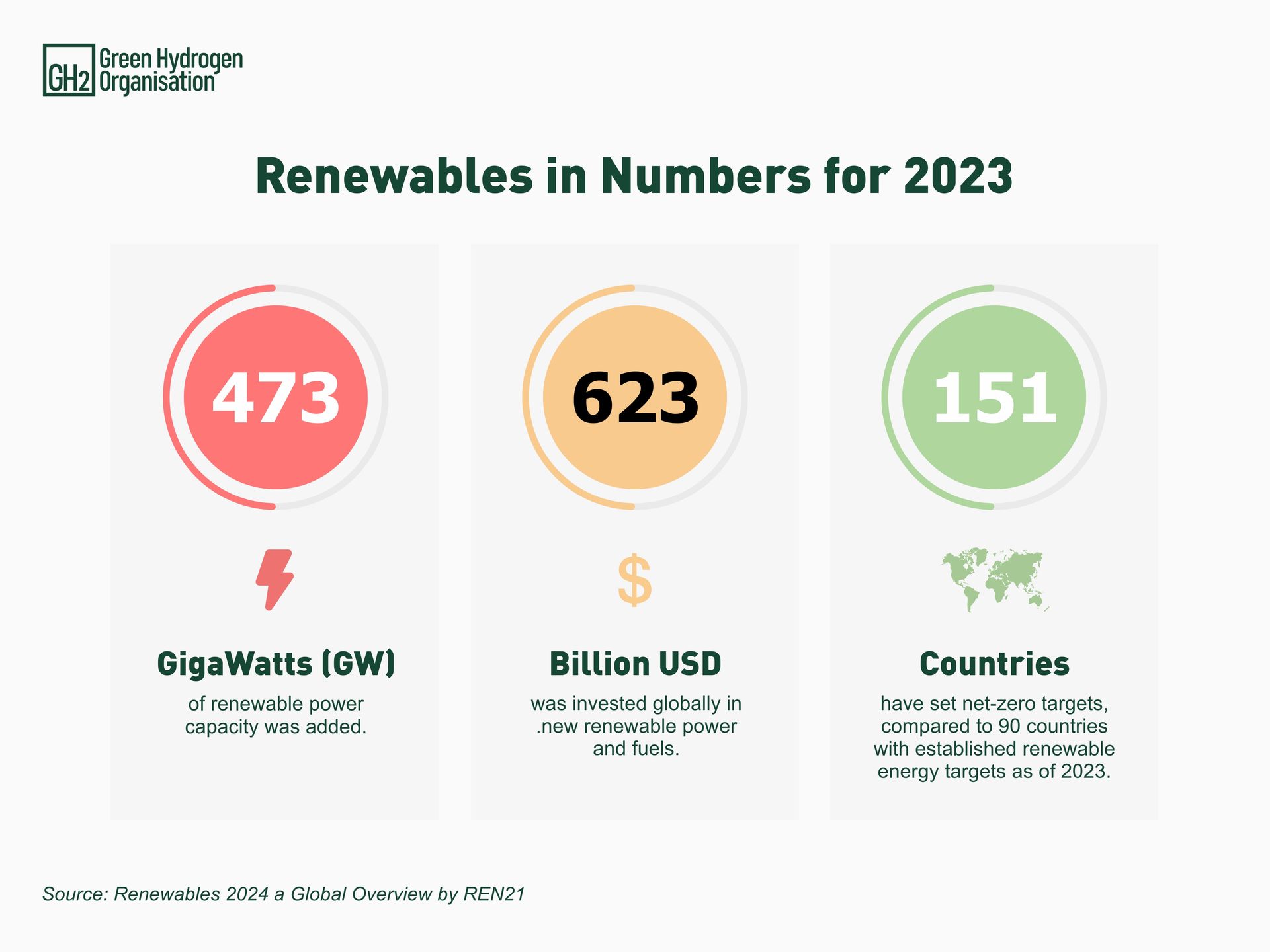